The Complexity of Designing Cannabis Facilities
By John Ritz
April 8, 2021 Architecture, Cannabis, Design, Uncategorized
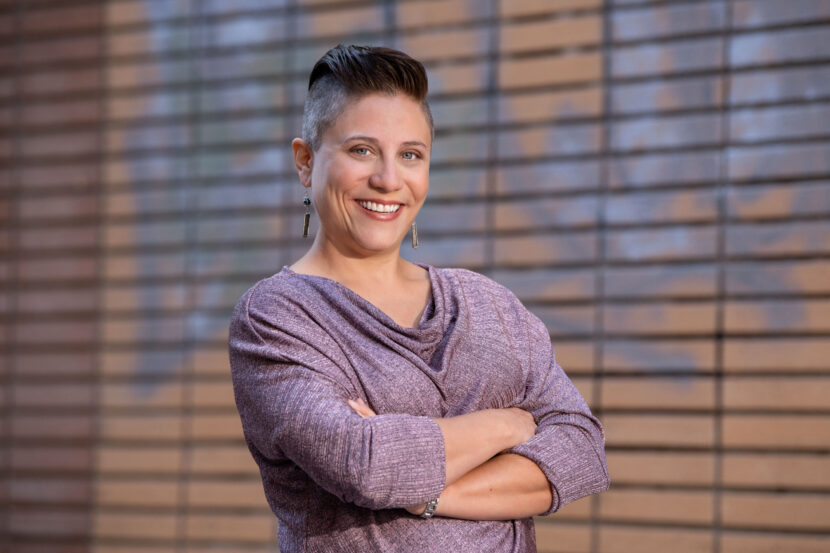
Knit Architect, Michelle Duranleau, AIA was recently interviewed discussing the complexity of designing cannabis facilities. Michelle and her team at Knit have been a part of these facilities from the cultivation facilities all the way through the dispensaries. The article can be found below.
The Complexity of Designing Cannabis Facilities
by Jean Leathers
The cannabis industry is a highly specialized agribusiness with complex facilities for growing, extracting, producing, testing, distributing and dispensing cannabis products.
“It’s a far cry from the days of basement or attic growing with a few dangling light bulbs and an open flame, “said Michelle Duranleau, the architect responsible for design of these facilities at Knit—an architecture design firm with offices in Las Vegas, Salt Lake City and Seattle. Duranleau and her team at Knit have developed a broad range of skills to accommodate the various design needs for vertically integrated facilities.
What’s Involved
Cannabis businesses that are vertically integrated entail a variety of environments including grow rooms, extraction labs, production rooms, distribution areas, and dispensary spaces. In addition, the complex often includes corporate offices, administrative spaces and security areas and distribution centers. Each of these spaces call for specific design requirements and understanding the flow and adjacencies as people and the plant move throughout the facility from growth to the dispensary is critical to creating an efficient, clean and well-functioning business.
Let’s take a look at each.
Grow
The Grow rooms, sometimes referred to as Cultivation, is where the cannabis plant is propagated. There are four classifications of rooms: Mother, Clone, Veg and Flower.
The Mother room is a secure room for the mother plants, designed with tight controls to prevent any kind of contamination or pesticides from damaging the plant. Once the mother plants are determined to be superior specimens, pieces are pruned and placed into small containers and moved into the Clone room. Once plants have grown again, they are placed in larger pots and moved into the Veg room. When the plants have grown large, they are moved to the Flower Rooms where they grow hardy and flower.
Each of these rooms is controlled separately having their own fertigation systems for water supply which contains nitrates, and other nutrients. Controls allow for different temperatures, minerals, vitamins, light and humidity to match the exact phase of growth.
Critical to the growth of the plant is the type of light applied and for how long. Growers each have own preferences depending on the strains of the plant they are growing. Adjustments are often made based on the look of the plant, its health and tumescence. Halides and LEDs are used alone or in combination throughout the grow process depending on the grower’s preference. Carbon dioxide is piped throughout each grow room and is controlled by the grower. To mix the air and heat from fixtures, all rooms must have fans and systems are designed to circulate the air appropriately.
Growers have their own preferences for temperature inside the grow facilities, whether a range from 65-73 degrees or 67-80, for example, depends on the strain of plant, the grower’s goals, and the plants’ reaction to the temperature. Humidity is also carefully maintained. The control system has sensors that measure relative dew point in order to automatically turn humidifiers or dehumidifiers on or off.
“The facilities are highly regulated with a combination of automatic and manual systems. The right mix of light, CO2, nutrients and so on is the grower’s secret sauce,” said Duranleau.
Trim and packaging occurs when the plants have been harvested.
According to Duranleau, “Bonsai ninjas go in and extract the bud and leaves, separating out the stems and twigs. Colorful, healthy buds are carefully selected and sent to packaging, while the rest is sent to the Extraction Lab.”
Extraction Labs
It is in the Extraction Lab that the process becomes hazardous. The chemicals used for extracting the oils from the plant include butane, ethanol and CO2—all extremely flammable. This hazard room requires a C1D1 explosion-proof design. Because of the molecular structure of butane, it can adhere to soft materials, so design requires hard surfaces throughout.
“What we really have is a clean room,” said Duranleau.
Ventilation is critical. In some cases, design calls for prefabricated extraction units, which are rated as a 2-hour fire enclosure. These are connected to the building’s air exhaust, water, power, and sprinkler system.
Once extraction is complete, the product is sent to Production for processing it into a variety of products.
Production Room
The products delivered to Production come from two stages of extraction. The first extraction produces THC. The second extraction produces CBD oil. These are then turned into products such as cartridges for vape pens, ingestibles, or lotions. The facility is designed to include a room for random testing of all products to ensure quality and confirm potency.
According to Duranleau, “Though the Food & Drug Administration is not involved at this time, we design to FDA regulations so that the facility can be certification-ready in the future. That way if the FDA or GMP—laboratory and pharmaceutical testing—or other agency inspects facilities down the road, our clients are compliant and won’t run into problems.”
Ingestibles such as chocolate and gummies require clean room conditions. Generally, these spaces require three-compartment sinks, lockable industrial freezers for storage, and regular temperature vaults. Food preparation could entail heat plates or working with gelatins; there are no open flames because of the flammable nature of extraction.
Once the products have been packaged, they are ready for Distribution.
Distribution
Many cities prohibit selling products where they are grown, so a full Distribution Center may be required. It bears noting that the entire building is designed with a single point of entry and a single point of exit. This makes the Distribution area one where security is of extreme importance.
This area includes a loading dock, warm and cold vaults for storing products, security equipment and personnel, as well as all required technical equipment for tracking inventory. This area is completely locked down and controlled.
Dispensary
The alternative way for products to exit the building is via a dispensary. While some states require dispensaries to be off site, some allow dispensaries within the grow facility. There are many types of dispensary fulfillment, with three being the most prevalent.
One is order out. An order is placed by phone or online, the order is fulfilled and then driven to the client.
The second way of dispensing the product is to make an appointment on site. The client arrives, signs in, has their ID verified, waits in the lobby until an associate comes to get the client, escorts them into the back, or simply goes over the product menu. The client selects products, the order is fulfilled in the back, the client pays and then exits.
The third option for dispensing is the most involved. In this scenario, the dispensary is set up for the client to visit a showroom and actually see, smell and inspect the product. Here the client enters as just described, then proceeds to the showroom with an associate. Products are displayed in cases as associates walk through the strains, discuss their effects and sell their goods. The client chooses products, the order is fulfilled, and a cash transaction takes place in the secured cash register area.
Executive Offices
Owners’ offices can be located on site within the building. Because these are headquarters offices where investors, high end clients and others come to conduct business, the office design needs to present the brand of the company and have a high level of finishes. Typically, there are individual offices, open work areas and a corporate conference room. A kitchen area and restrooms are included.
Duranleau said, “The executive spaces are a joy to design. We love the challenge of collaborating with our clients to express who they really are through the physical spaces where they work. Helping clients to create their branding expression through interior and exterior design—it’s so satisfying when you see it all come together.”
Central Plant
The Central Plant is often a separate building on site. It is the heart and soul of the building designed to hide the major HVAC equipment like chillers, boilers and other mechanical equipment required to control the environment inside the main building.
Exterior Building Design
Remembering that these vertically integrated buildings are the headquarters for the cannabis business, exterior design is important. First impressions of investors, collaborators and clients means that design, while not elaborate, must be deliberate in presenting the face of the company and reinforcing its brand.
Design of cannabis facilities means that architects need to hone their skills from coordinating with complex engineering techniques for growing plants, to significant security measures, from creating clean facilities, to expressing corporate identity and branding and making a first class first impression.
“Cannabis facilities are truly creative challenges. We love working on them,” said Duranleau.
It’s easy to see why.
To learn more about Knit’s experience with Cannabis Facilities, click here.